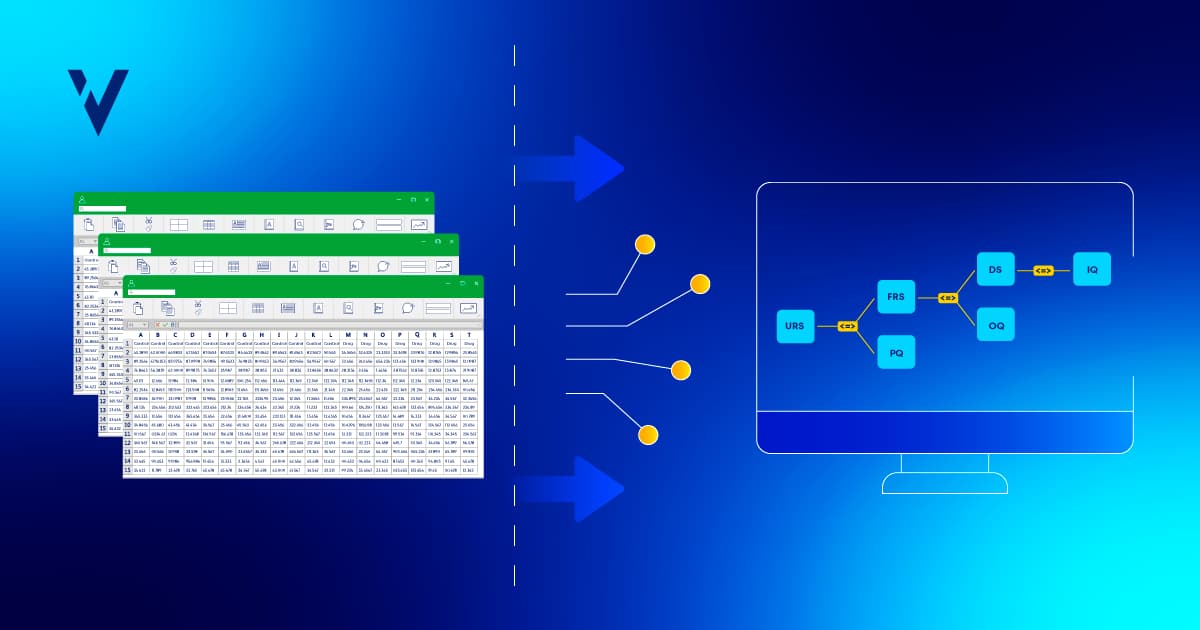
The Benefits of Automating Your Requirements Traceability Matrix
Automate your requirements traceability matrix to improve efficiency, reduce compliance risks, and streamline validation for better audit readiness.
May 8, 2025 10:00:00 AM | Learn how spreadsheet chaos undermines Quality by Design in pharma—and how digital QbD platforms support CMC manufacturing and development.
Root-Cause Analysis
Finding the Root Cause in mAB Production: a ValGenesis Story
Learn how we helped a customer find the root cause of a problem in monoclonal antibody (mAB) production and become stronger.
Written by
Sofia Santos
Process Digitalization
How to Accelerate Process Scale-Up With Effective Tech Transfer
There's a need to accelerate pharma product development and process scale-up. Having an effective tech transfer strategy can help you.
Written by
Sofia Santos
Quality Risk Management
Risk and Data as Knowledge Enablers: a Lifecycle Approach - ValGenesis
Read the industry insight on the topic of Quality Risk Management
Presented by
Sandra Silva