Benefits this Solution Provides
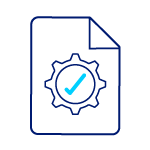
Generate Validation Plans Automatically
Auto-generate the validation plan and summary with precise, clear metrics.
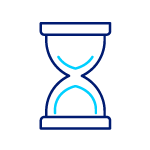
Ensure Timely Planning and Documentation
Stay on task with systematic scheduling and task notifications.
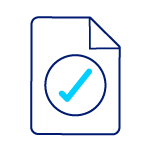
Manage Critical Documents
Manage layout drawings, P&IDs, schematics, and software logic/algorithms in one location.
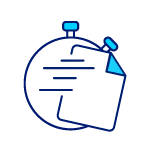
Leverage the Power of Automated Test Scripts
Bring efficiency and speed to document authoring using a decision-tree-based process.
_________
_________
_________
See how ValGenesis can support your digital transformation.